Capables d’embellir tout espace grâce à leur beauté intemporelle, les carreaux de ciment ont connu un regain de popularité ces dernières années. Bien que la méthode de fabrication ait été inventée à la fin du 19e siècle, elle n’a subi aucun changement. Nécessitant une grande précision ainsi que de la justesse dans les dosages, le procédé est extrêmement technique et chaque carreau est une pièce unique. Déco Mosaic vous explique comment sont fabriqués les carreaux de ciment.
Tour d’horizon des matériaux utilisés pour la réalisation des carreaux de ciment
L’obtention de ces magnifiques carreaux au charme rétro nécessite l’utilisation de matériaux bien spécifiques. De nombreux éléments entrent dans la fabrication d’un carreau de ciment de qualité :
- ciment Portland : constitue la base du produit et leur permet d’acquérir la solidité nécessaire,
- sable : crée cette texture caractéristique des carreaux de ciment,
- pigments : ajoutés au mélange afin d’obtenir des motifs uniques.
L’eau est également un élément indispensable dans le processus de fabrication des carreaux de ciment, car elle contribue au durcissement du revêtement.
Les étapes de fabrication des carreaux de ciment
La fabrication des carreaux de ciment suit un processus précis, alliant savoir-faire traditionnel et attention aux détails. Chaque étape contribue à garantir leur robustesse, leur esthétique et leur longévité. Cela rend ces carreaux idéaux pour des aménagements durables et élégants.
Le nettoyage du moule et la pose du séparateur
Pesant près de 15 kg, le moule utilisé pour la fabrication des carreaux de ciment est en acier. Ce dernier est composé d’un cadre, d’un tampon et d’un fond. Avant de procéder à cette technique, il doit être nettoyé, graissé et lustré afin de faciliter le démoulage.
Un séparateur en laiton doté de cloisons verticales qui forment des alvéoles est ensuite posé au fond du moule. Ce dernier permet de couler les différentes couleurs du carreau (bleu, noir et blanc, rouge, vert, ou encore gris). Le diviseur en laiton fait l’objet d’un contrôle fréquent. Sa planéité et son adhérence au fond du moule sont ainsi assurées.
L’application de la couche de surface et le retrait du diviseur
Le mortier de couleur représente la couche de surface dans le diviseur. Pour le couler, un biberon ou une louche sont utilisés. Le moule est ensuite secoué afin de garantir une répartition uniforme de la préparation dans le séparateur.
Le mortier utilisé se compose de ciment blanc, de poudre de marbre et de pigments. La couche de couleur qui est très liquide s’étale sur quelques millimètres au fond du moule. Une fois les couleurs versées, le séparateur est délicatement retiré. Lors de cette étape, les couleurs se mélangent entre elles. La couche déposée au fond du moule qui forme la surface du carreau reste cependant stable. Le mortier liquide est ensuite cristallisé avec un mélange de sable et de ciment sec.
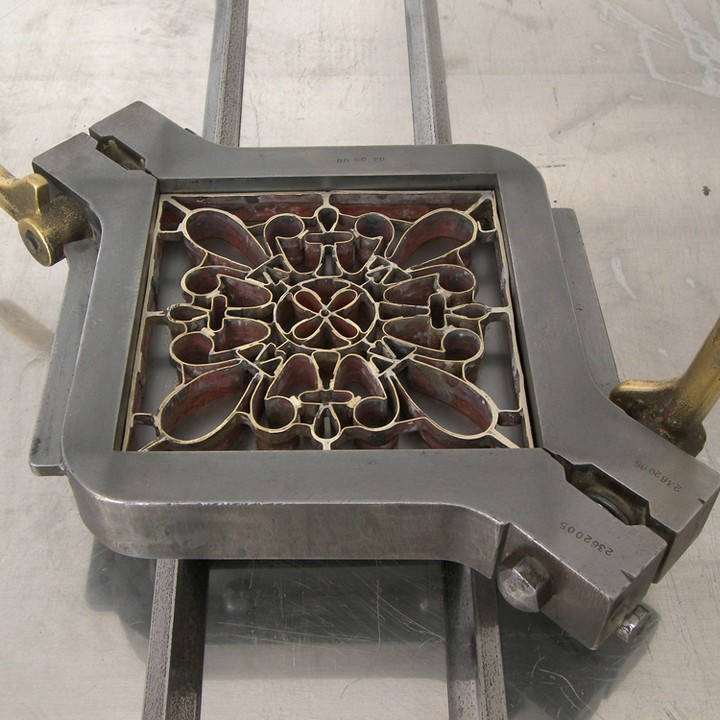
Le remplissage du moule et le passage à la presse
À cette étape, le moule est rempli avec un mortier grossier composé de ciment et de sable. Lorsque le cadre est plein, il est fermé et un motif en relief est imprimé à l’aide d’un tampon. Les cadres qui sont dotés d’une charnière à l’extrémité d’une des diagonales et d’un système de réglage permettent une fermeture rapide ainsi que l’extraction du produit fini.
Vient ensuite la phase de presse où l’excès d’eau présent dans la couche colorée s’intègre dans la couche de structure. Dès lors, la teneur en eau ainsi que la plasticité de toutes les couches deviennent homogènes.
L’extraction du moule et l’immersion
La phase d’extraction du carreau de ciment commence par le retrait du tampon, le déverrouillage du moule et le retrait du cadre. Le démoulage requiert de la technique, car le carreau n’est encore qu’un agglomérat de ciment et n’a aucune résistance. Vu la délicatesse de cette phase, il est impossible d’automatiser le processus de fabrication de ce revêtement.
Après l’extraction du produit fini, il est posé sur une base bien nivelée et laissé au repos pendant 24 heures. Le carreau est ensuite transporté dans un local où il est immergé dans un grand bac d’eau. L’hydratation de l’agglomérat de ciment permet de garantir une bonne prise ainsi qu’une parfaite fragmentation.
Le séchage
Le séchage constitue une étape primordiale dans la fabrication des carreaux de ciment. Une fois retirés de l’eau, les carreaux sont délicatement disposés sur des étagères dans un espace à l’abri des variations de température et d’humidité (le carreau de ciment est sensible à l’humidité, d’où la nécessité de l’imperméabiliser).
Ce repos prolongé, d’environ quatre semaines, permet au ciment de durcir petit à petit. Il garantit une solidité et une résistance optimales. Une fois le séchage complet, les carreaux sont soigneusement vérifiés, nettoyés si nécessaire, puis emballés avec attention pour préserver leur intégrité jusqu’à leur arrivée chez le client.